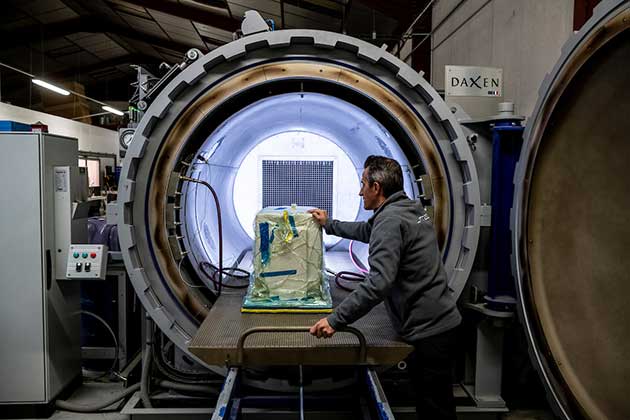
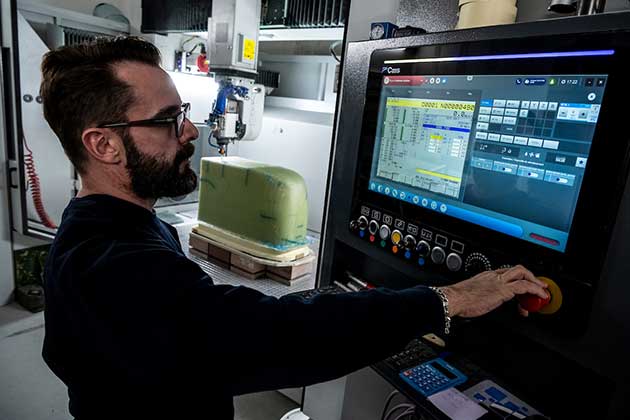
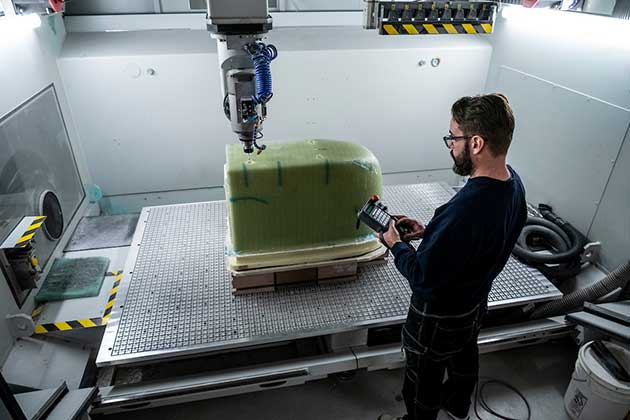
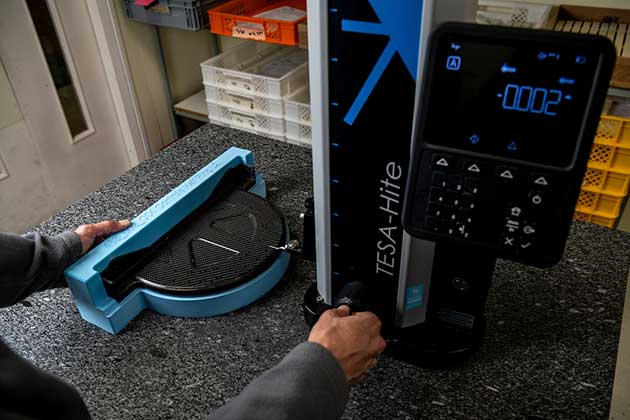
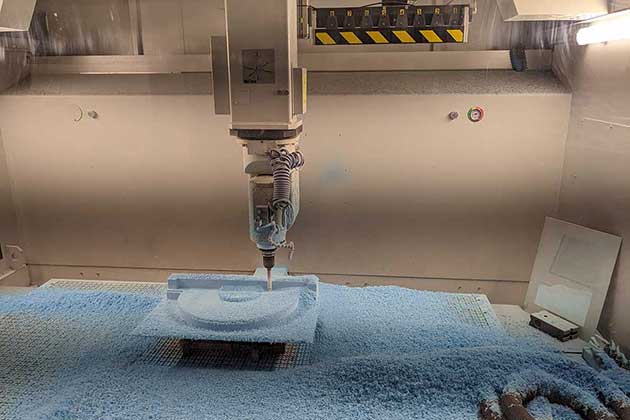
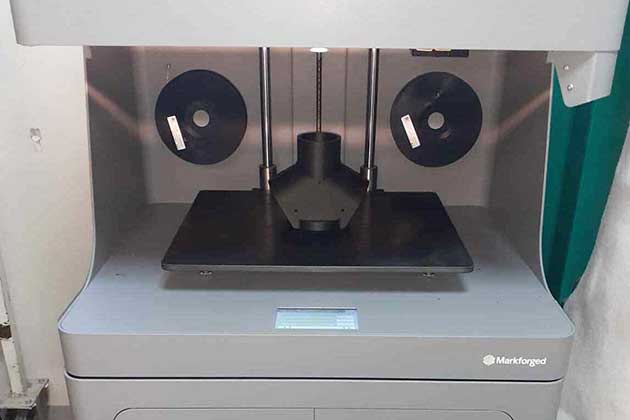
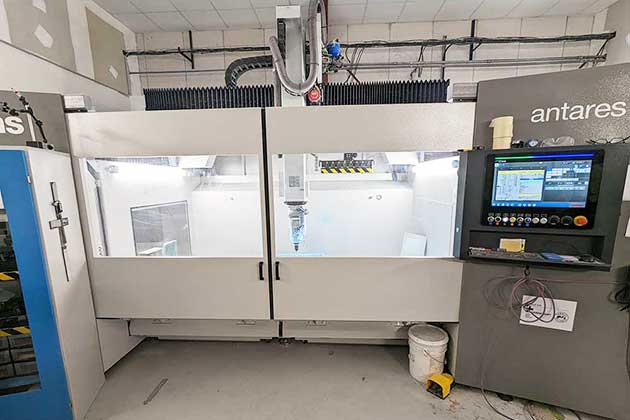
Atem Composites
Les équipes d'Atem Composites vous accompagnent dans la conception et la réalisation de vos pièces mécaniques en matériaux composites et les outillages associés
Atem Composites, anciennement VN Composites, est une société du groupe Atem depuis juillet 2020. Le savoir-faire de l'entreprise repose sur sa maîtrise de nombreux procédés de fabrication de matériaux composites, sur l’ingéniosité et la polyvalence de ses équipes, sur notre parc machines et outils de production de haut niveau.
De nombreuses entreprises nous choisissent pour faire du prototypage de leurs pièces qu’aucun autre acteur n'a été en capacité de réaliser la prestation complète, de la reprise de la CAO, à la conception des outillages, à la réalisation des pièces en vue de leur qualification et leur passage en série, avec en plus l’ajout de la prestation de peinture de finition si nécessaire.
Nous sommes consultés et retenus sur des projets qui constituent généralement de réels challenges techniques !
Nous réalisons une analyse globale de votre projet. Nous y répondons en définissant le meilleur procédé pour réaliser les pièces avec des performances reproductibles. Nous déterminons les matériaux et le meilleur procédé de fabrication en fonction de vos critères de performance attendus.
Nous intervenons généralement sur votre conception 3D afin de rendre votre pièce plus facile à produire en matériaux composites, quelle que soit sa complexité. Notre objectif est de vous proposer des pièces plus légères qu’en matériaux métalliques, performantes sur le plan mécanique (résistance à la fatigue, capacité à absorber des chocs…), esthétiques et si possible plus respectueuses de l’environnement.
Nous nous sommes donnés les moyens d’avoir une très bonne maitrise des procédés avec un parc industriel adapté pour les mettre en œuvre afin de répondre aux défis et autres « moutons à cinq pattes » de nos clients.
Nous intervenons sur toutes les étapes de la vie de vos pièces à partir de votre CAO jusqu’à sa qualification, les premières de série, voire la série en fonction de vos besoins et de vos critères de fabrication. À titre d’illustration, nous avons déjà produit plus de 20 000 barreaux FLASH pour le Sonar FLASH de Thales DMS.
Notre savoir-faire repose sur la maîtrise de techniques de fabrication complexes, notamment sur la bonne association entre fibre et résine (quantité et type) qui permet d’obtenir les performances mécaniques attendues.
Nous réduisons significativement la masse de vos pièces. Nous avons ainsi permis à l’hôtellerie de luxe de remplacer des plateaux en argent à l'origine de troubles musculosquelettiques chez le personnel par des plateaux en carbone.
Nous avons développé une trappe allégée de 65 kg par rapport à celle habituellement utilisée par EDF dans ses centrales hydrauliques. Un allègement de masse qui permet de la manipuler avec moins de personnel deux opérateurs au lieu de quatre et plus aucun moyen de manutention spécifique.
Nos BE en hyperfréquence et composites coopèrent pour vous proposer la conception et la réalisation de radômes spécifiques. Nous avons développé un démonstrateur de tiroir hyperfréquence en fibre de carbone et résine époxy pour réaliser des gains de masses significatif (> 30%) qui intègre un bronze mesh.
Nos BE en électronique et composites ont par exemple coopéré pour proposer des protections d’électronique en matériaux composites pour gagner en légèreté, proposer des consoles avec une structure composite…
Nous proposons des structures en carbone garantissant la stabilité dimensionnelle des pièces finales quelles que soient les températures extérieures qui peuvent être extrêmes (porte capteur de décompte de particules - CERN). Nous avons aussi réalisé des pièces pour des radiotélescopes qui ont besoin d’une précision extrême dans leur pointage (éviter toutes dilatations…)
Nous poussons loin la conception des outillages pour réaliser des pièces en monobloc afin d’éviter toute fragilité structurelle. C’est le cas par exemple pour un collecteur d’admission où nous sommes les seuls à avoir réussi à sortir la pièce en monobloc.
Nous sommes capables de repousser les limites de l’état de l’art en poussant à l’extrême le taux matrice/fibre pour accroitre la transparence, mais aussi pour conserver un son le plus pur possible avec seulement un pli de carbone pour réaliser des ligatures haut de gamme pour les clarinettes et saxophones.
Nous sommes de plus en plus sollicités par le secteur du luxe et de l'hôtellerie qui plébiscite le caractère esthétique du carbone, ainsi que sa légèreté. Ce procédé est utilisé aujourd’hui pour réaliser des supports de carter pour le comptage de particules au CERN, des ligatures pour clarinettes et saxophones, également pour le système de désignation d’objectif d’urgence pour les marines… Nous sommes de plus en plus sollicités par le secteur du luxe et de l'hôtellerie qui plébiscite le caractère esthétique du carbone, ainsi que sa légèreté.
Nous maitrisons une large palette de procédés de fabrication :
Mise en forme de pré-imprégnés
Infusion
Composite Moulé par Compression,
Strat au contact
Infusion
Resin Transfer Molding (RTM)
Fabrication additive composite
L’opération de drapage consiste à découper des plis de matière première, appelée pré-imprégnés, et de les draper manuellement dans un moule (conception et fabrication par Atem Composites) qui apportera la forme de la pièce. Notre savoir-faire nous permet de définir l’orientation des plis durant le drapage en fonction des performances mécaniques recherchées. Les méthodes de cuisson sont sous vide et généralement en autoclave sous pression à l’aide d’une vessie (baudruche) réalisée en interne, sous presse via plateau chauffant.
Les avantages de ce procédé sont les suivants :
Grande liberté dans la forme des pièces
Très bonne maitrise du ratio fibre/matrice, excellentes performances mécaniques.
Mise en forme de pré-imprégnés
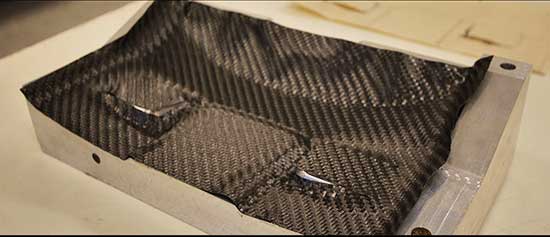
CMC : Composite Moulé par Compression ou SMC (Sheet Molding Compound) :
Atem Composites a développé un process spécifique de fabrication pour ce matériau, réalisé avec un composite carbone quasi isotropique de haute résistance.
Le principe consiste à mettre en forme sous haute pression un tapis de fibre disposé aléatoirement dans le plan afin d’obtenir une pièce volumique.
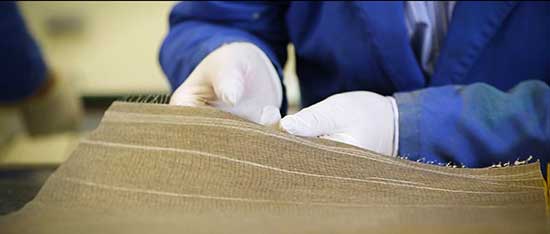
Les avantages de ce procédé sont les suivants :
Cadences de moulage élevées à Temps de cycle court = Réduction du coût de fabrication des pièces séries
Grande possibilité de formes complexes de type nervures et optimisation du design des renforts
Comportement mécanique isotropique de la pièce
Pièce sortie de moule en côtes finies
Excellente reproductibilité des pièces
Résistance en compression et en traction
Intégration des fonctions sur une même pièce (types inserts noyés)
Orientation des fibres lors de la mise en œuvre à amélioration de la tenue transverse en fonction de l’épaisseur de la pièce et de l’organisation isotropique des fibres
Proportion en fibre varie de 10% à 60% selon les cas d’applications
Très bonne tenue à la température selon la matrice (120°C à 260°C)
Bon état de finition de la pièce en sortie de moulage
Infusion
Le procédé d’infusion consiste à mettre en place des tissus secs sur un moule à l’aide d’une bâche à vide. La résine est ensuite drainée par l’action du vide afin d’imprégner les tissus. Un avantage notable de ce procédé est qu'il est réalisé à température ambiante.
Nous utilisons aujourd’hui ce procédé pour la réalisation de tables de travail pour les équipes de production d’antennes sous-marines de Thales Defense Mission Systems (DMS). Ces goulottes sont revêtues d’un gelcoat qui permet aux opérateurs de travailler sans risque de transmettre des décharges électrostatiques aux produits.
Les avantages de ce procédé sont les suivants :
Possibilité d’obtenir des pièces sandwich en une seule opération « one-shot »
Bonne reproductibilité des pièces
Maitrise du ratio fibre/résine comparé au procédé de stratification au contact
Obtention d’une pièce avec une seule face lisse
Le procédé est en moule fermé donc pas de dégagement de vapeurs nocives
Réalisation de pièces de grandes dimensions
Notre démarche est aussi de réduire notre empreinte environnementale.
Nous réalisons nos projets dans une logique d’éco-conception. Nous utilisons dans la mesure du possible des composants biosourcés (comme la fibre de lin, résine bio ).
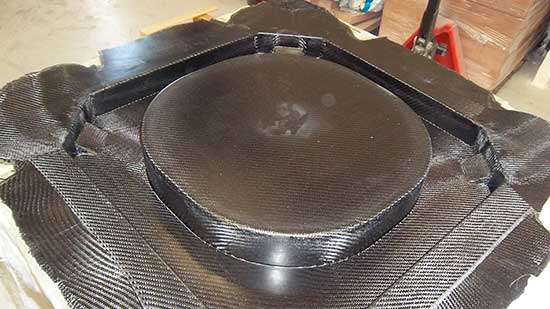
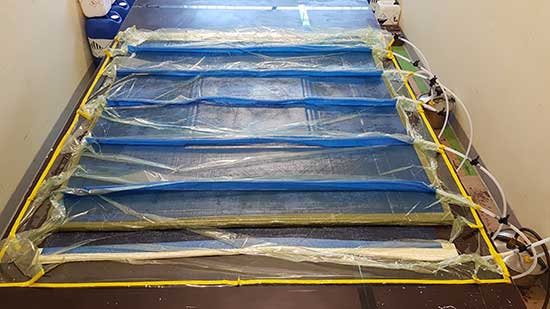
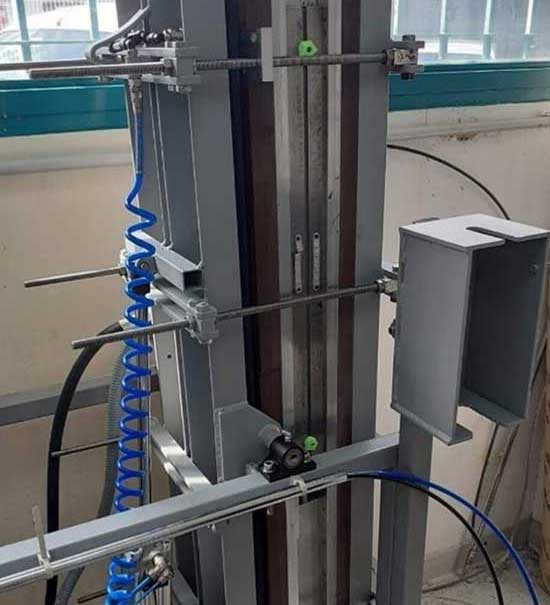
RTM : Resin Transfer Molding
Le procédé RTM consiste à l’injection sous basse pression d’une résine à travers des tissus secs mis en place dans un moule fermé.
Atem Composites possède une salle dédiée à ce procédé de fabrication, afin de maitriser avec un grand degré de précision les paramètres de température et d’hygrométrie, influant sur la qualité de la pièce.
Nous utilisons aujourd’hui ce procédé pour la réalisation des barreaux FLASH qui sont des « radômes acoustiques » pour le programme SONAR FLASH de Thales DMS. Notre produit apporte de la protection mécanique aux senseurs tout en laissant passer les ondes acoustiques. Nous avons poussé l’état de l’art très loin avec un ratio très important de résine afin d’être le plus transparent possible aux ondes acoustiques.
Ce procédé permet la maitrise des éléments suivants :
Cadence de moulage supérieure au process d’infusion (plateau chauffant permettant une réticulation plus rapide)
Possibilité d’obtenir des pièces creuses via l’utilisation d’un noyau
Excellente reproductibilité des pièces
Maitrise optimisée du ratio fibre/résine comparé au procédé d’infusion sous vide
Obtention d’une pièce avec deux faces lisses (contre une seule en infusion)
Obtention de pièces en cotes finies
Le procédé est en moule fermé donc pas de dégagement de vapeurs nocives et donc procédé bien meilleur sur le plan HSCT
Réalisation de pièces de petites et grandes dimensions
FABRICATION ADDITIVE COMPOSITE
Atem Composites a investi dans la machine MarkForged X7 qui lui permet de proposer des pièces composites (matrice avec renforts localisés de fibres longues) avec des performances mécaniques adaptées pour de très nombreuses applications. Les avantages de ce procédé sont la réalisation de pièces composites sans l’utilisation de moules, avec une maitrise répétable du temps de production. Ce procédé est Idéal pour des petites et moyennes séries sans aller chercher des pièces de grandes dimensions.
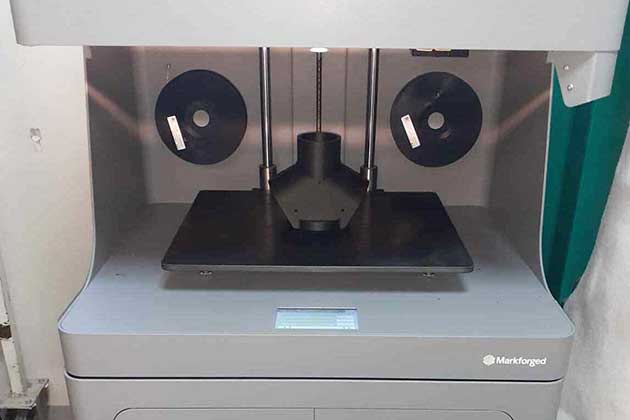
Chez Atem Composites, nous vous garantissons des challenges techniques que vous résoudrez en équipe (Bureau d’études et atelier travaillent main dans la main vers de nouveaux produits pour nos clients). Nous vous promettons des missions stimulantes et polyvalentes. Vous serez amenés à tester tous nos procédés, à manipuler différentes machines, à créer les pièces les plus complexes…
Et si vous aussi, vous participiez à la réussite des programmes de défense ? La minutie est une seconde nature chez vous ?
Vous souhaitez valoriser cette aptitude au sein d’un métier, d’une entreprise et d’un groupe passionnant ?